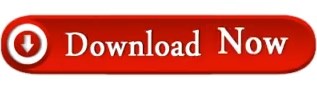

This model is unique in the open literature and comprises the major contribution of this thesis. Realistic component-to-component variations, and static and dynamic crankshaft imbalances may be specified. Thus, the modeling work is based on rigid-body dynamics and has led to an analytical simulation of engine dynamics and vibrations having seven degrees of freedom that account for the three-dimensional motion of the engine block, crankshaft, pistons, and connecting rods. Projection of the running engine data onto the measured engine modes showed that more than 80% of the engine's vibration output from 0 to 200 Hz could be described by rigid body motions.
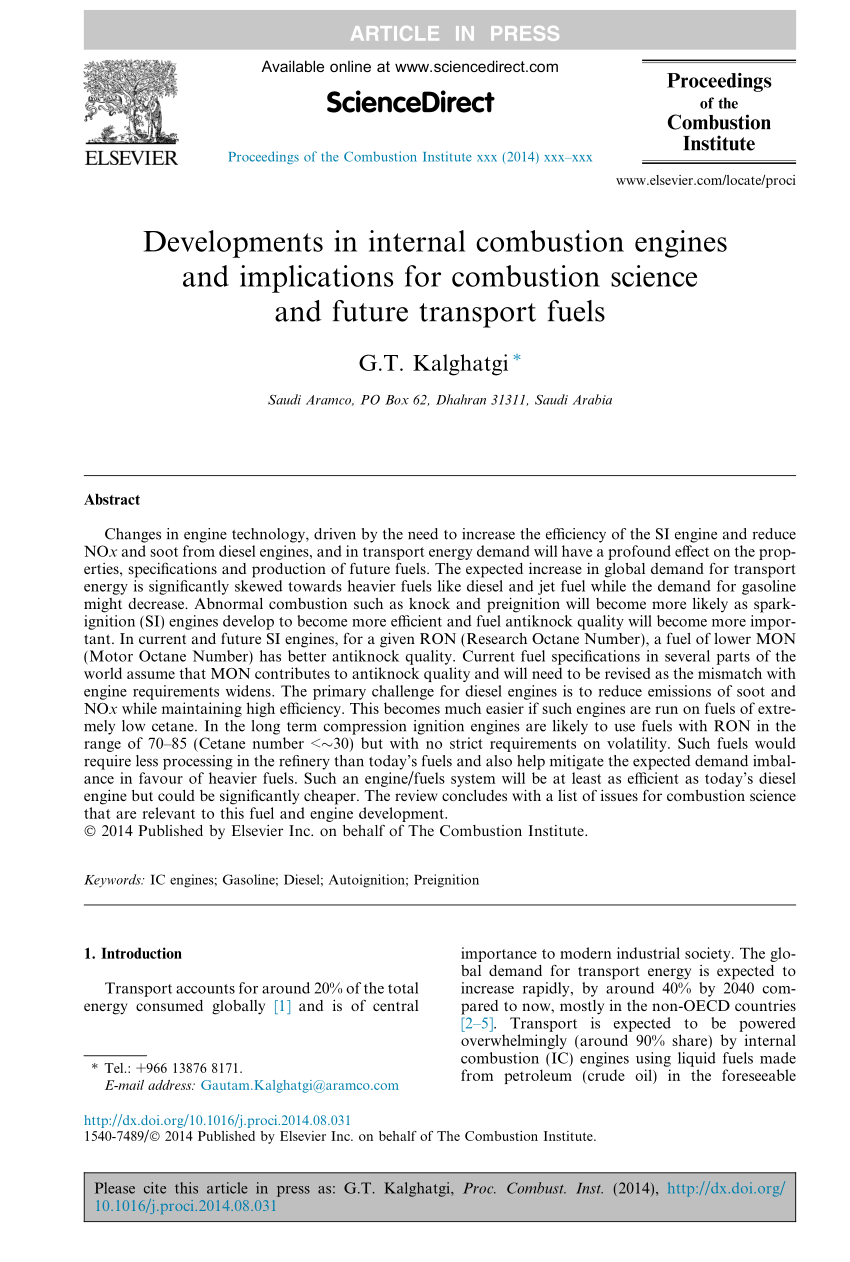
Data was collected from the quiescent engine via impact testing to determine its rigid-body modal response, and from the operating engine to determine the vibration loads transmitted through the engine mounts.
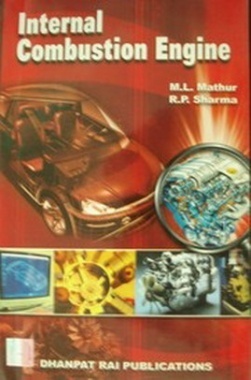
The experimental work is based on time-resolved force measurements made at the mount locations of an in-line heavy-duty Diesel engine having six cylinders and a nominal rating of 470 horsepower. Here, a unique time-domain model is developed for predicting IC engine dynamics and vibration from the type of parametric data commonly available during preliminary design. Excessive vibration adversely impacts vehicle durability, customer perceptions of quality, and vehicle operator readiness. IC engines are a primary vibration source in all types of vehicles. AbstractThis thesis describes a combined experimental and modeling study focused on piston-driven internal combustion (IC) engine dynamics and vibration.
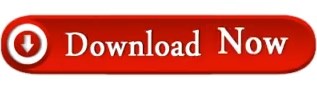